User interfaces and experiences are key factors in any interactive product and often requires an understanding of human factors and design to get it right. One of my favorite visual examples of this is to the right.
​
Anticipating
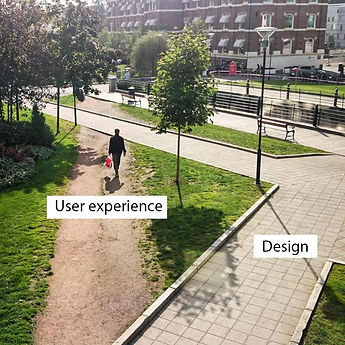
seen many industry concept artists that have a mastery of digital drawing and painting techniques, design, composition, lighting, and storytelling (often overlooked). There are many demonstrations and tutorials that can be found on youtube, and online subscription services that are amazing and useful for those learning the craft.


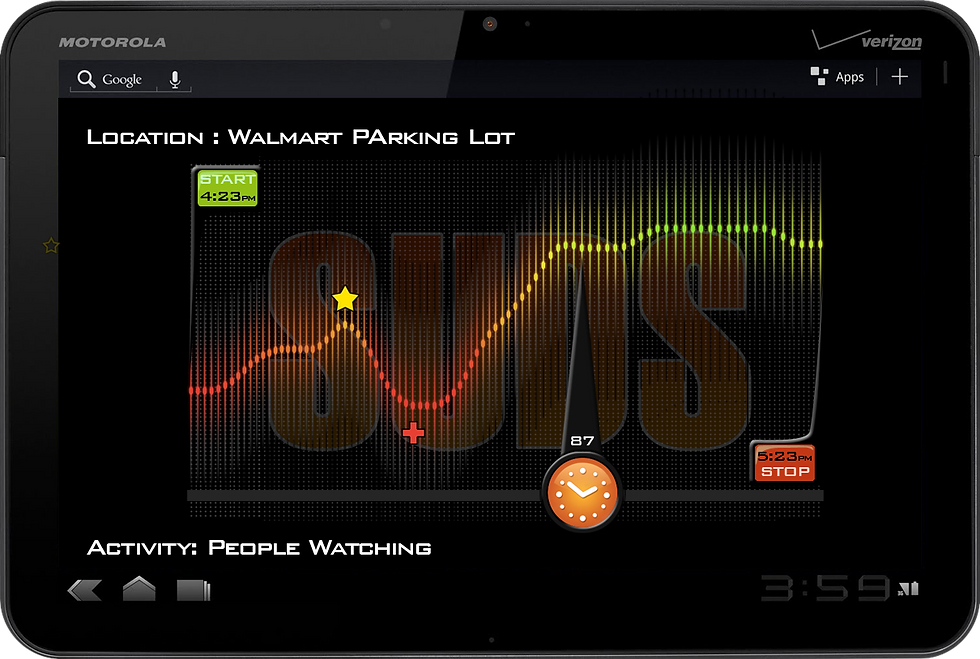
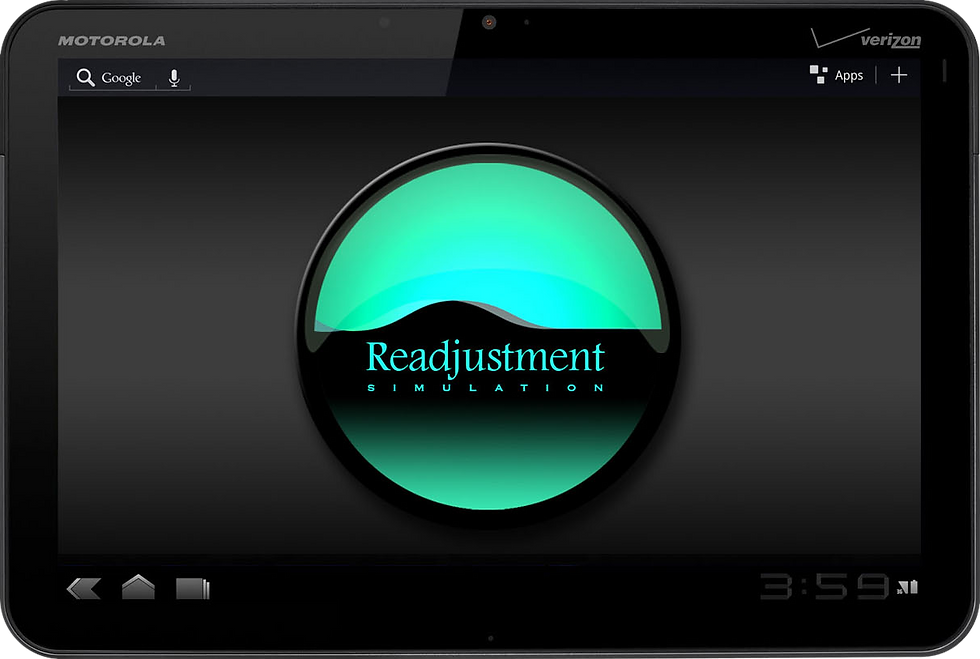
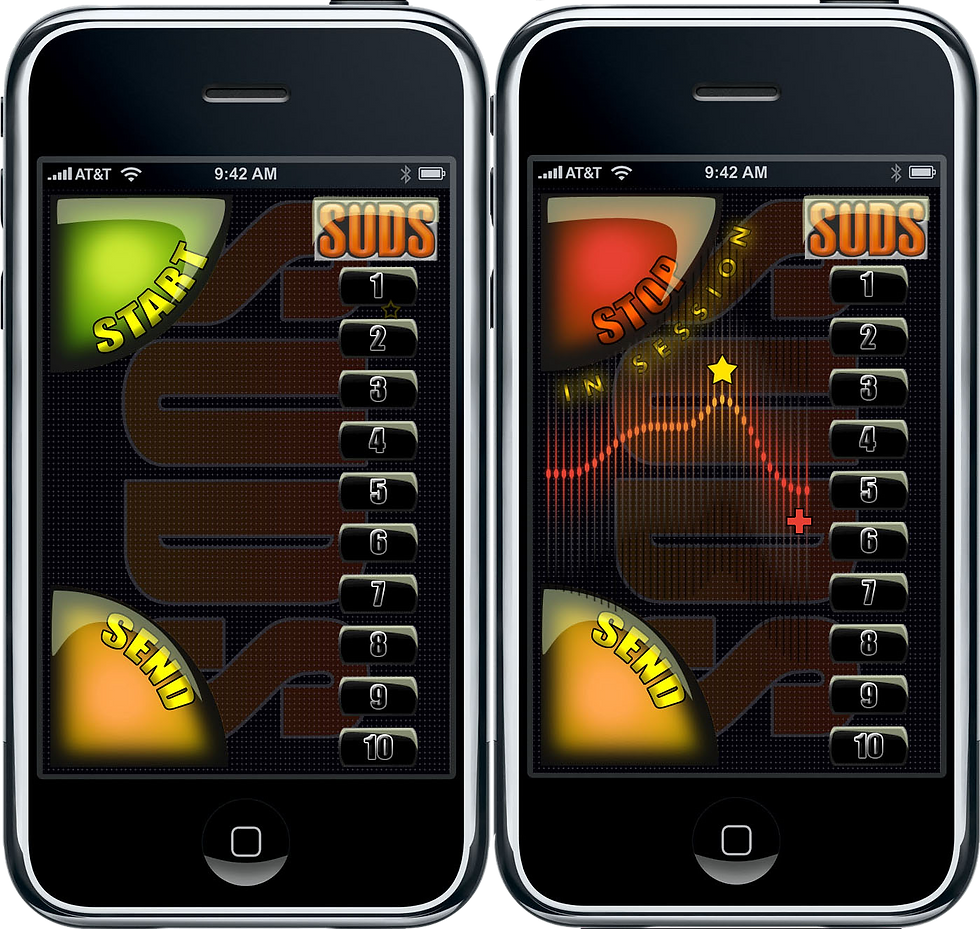


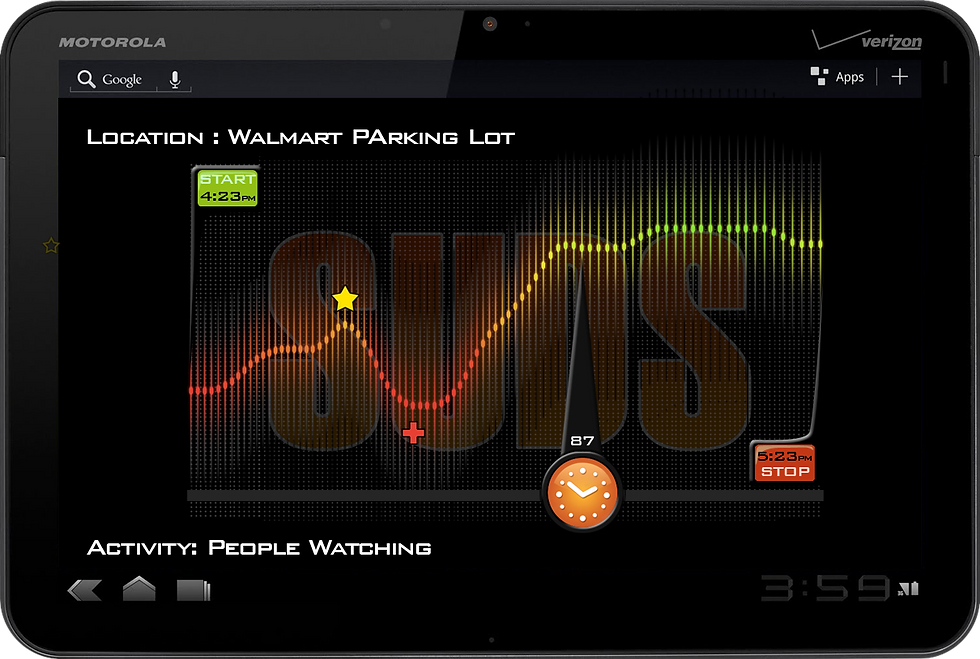
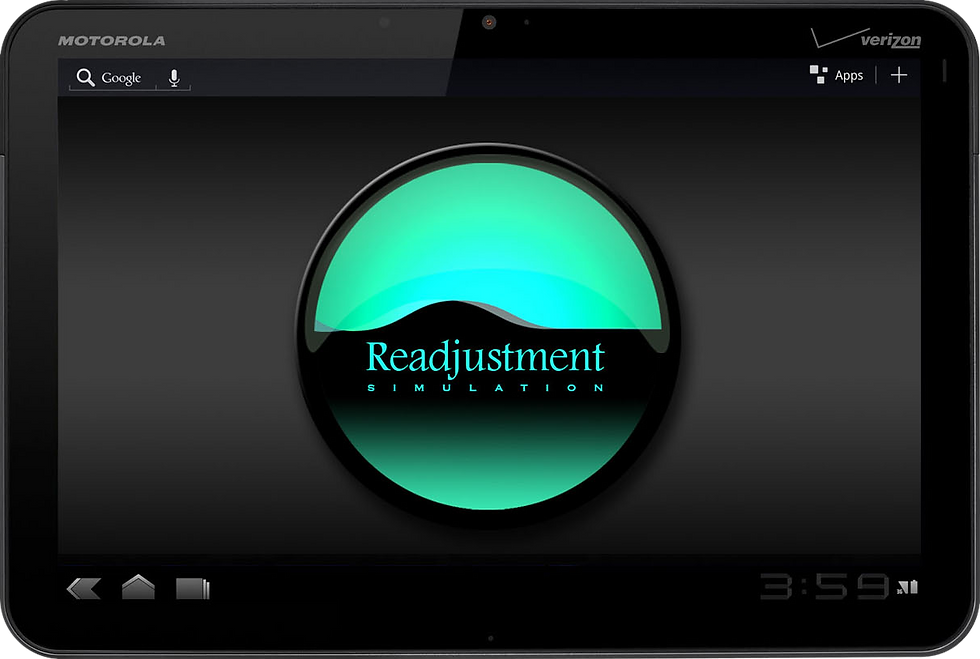
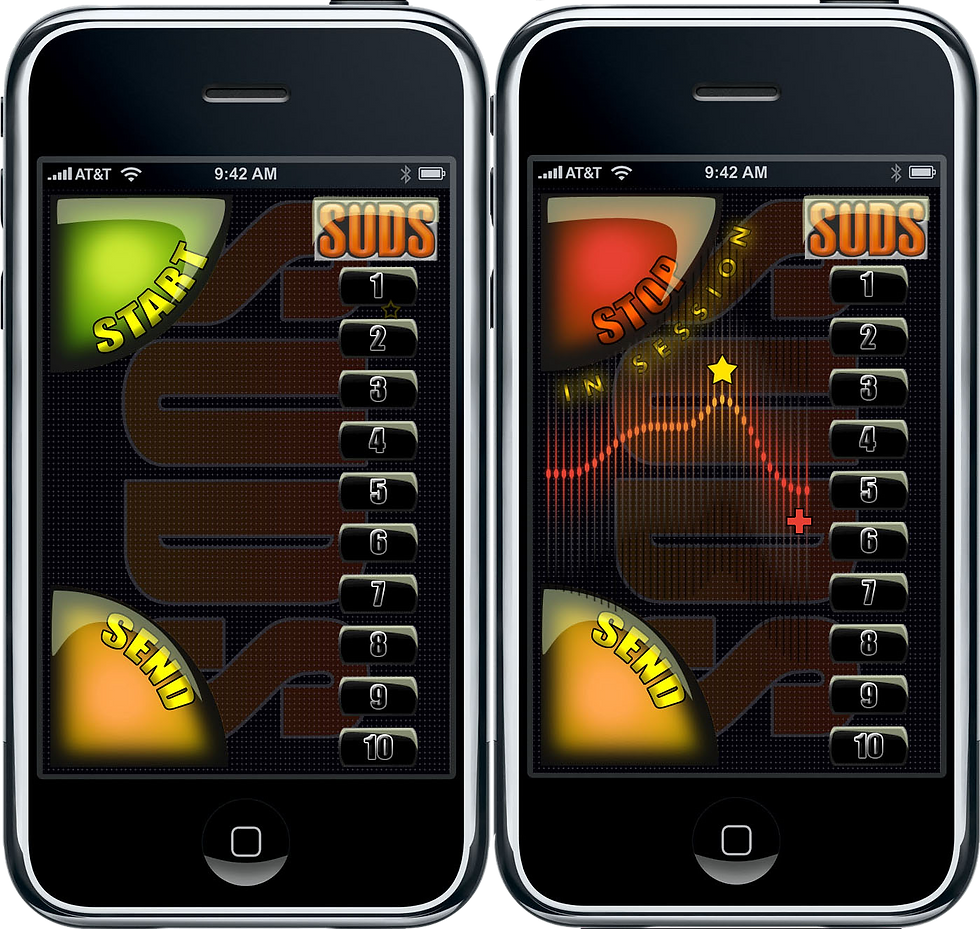



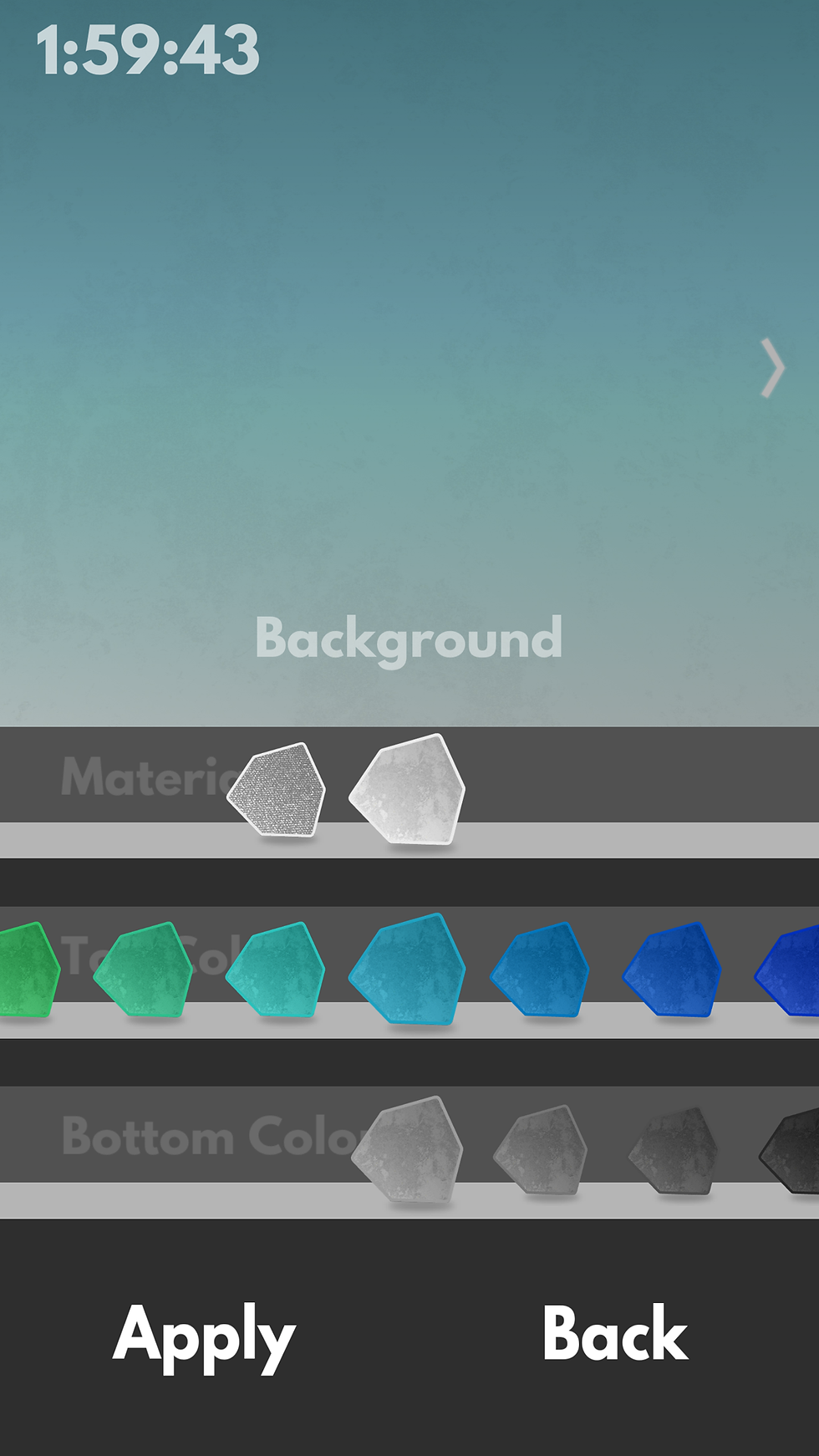
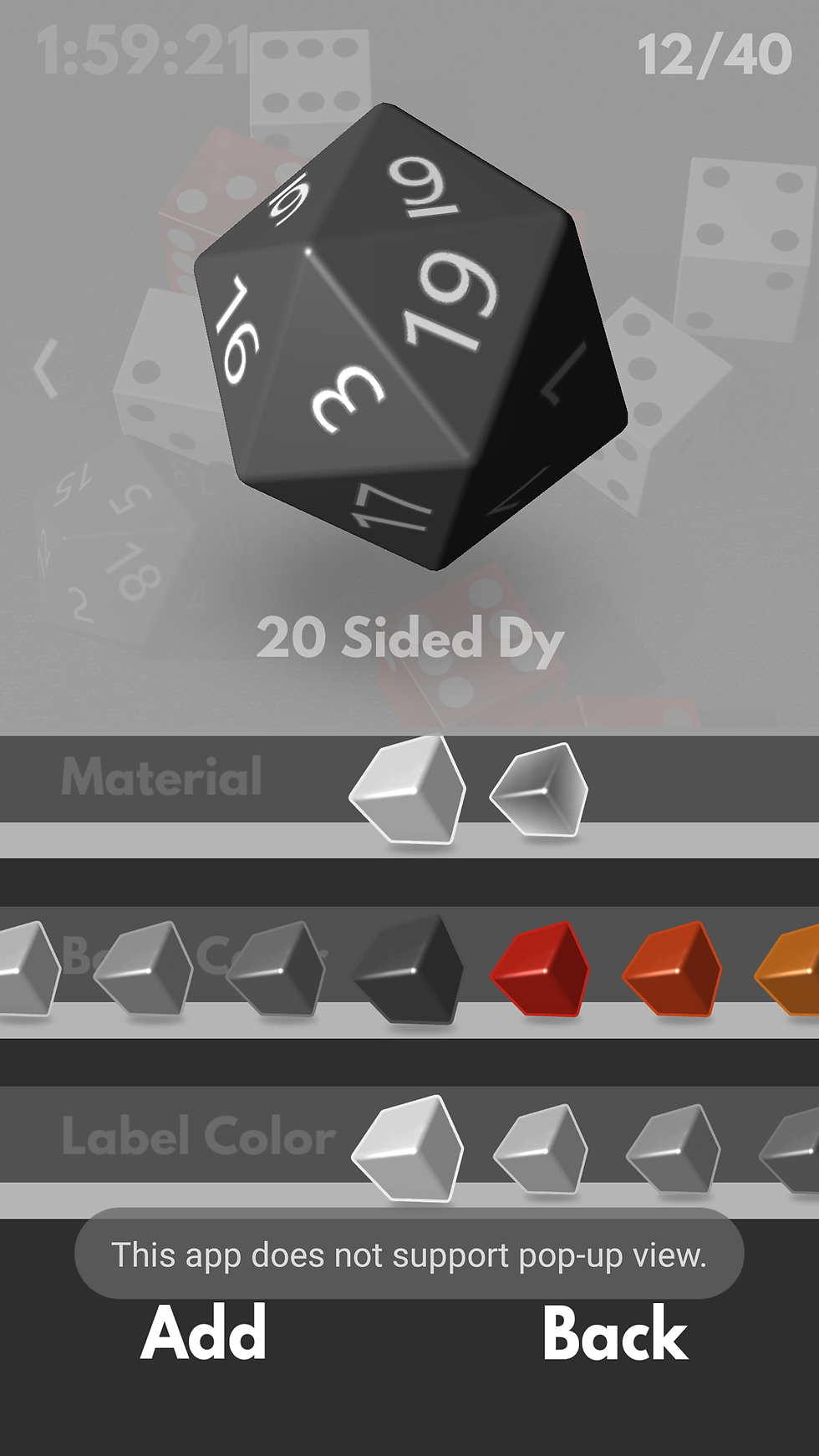
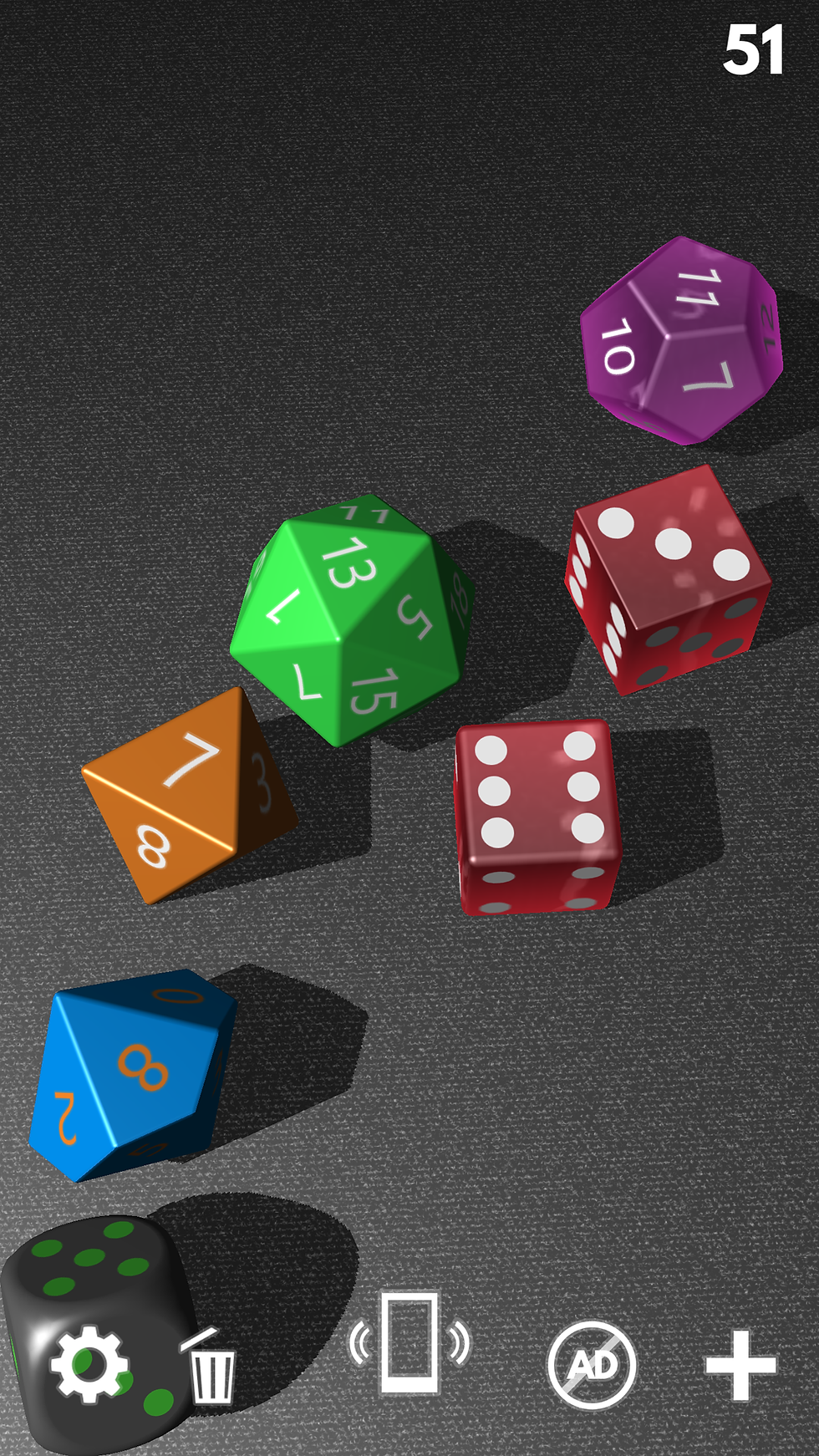
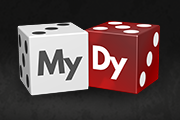



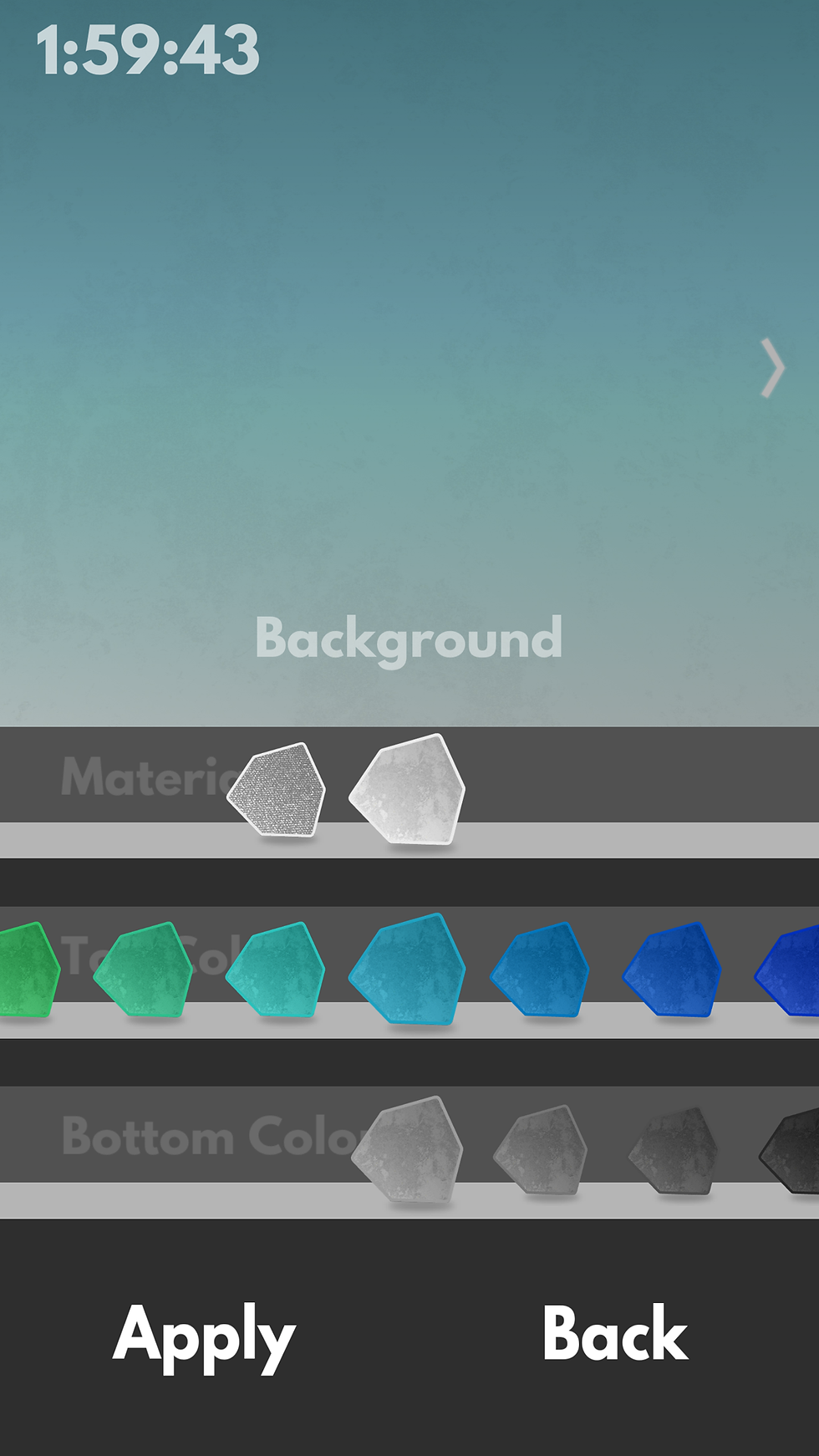
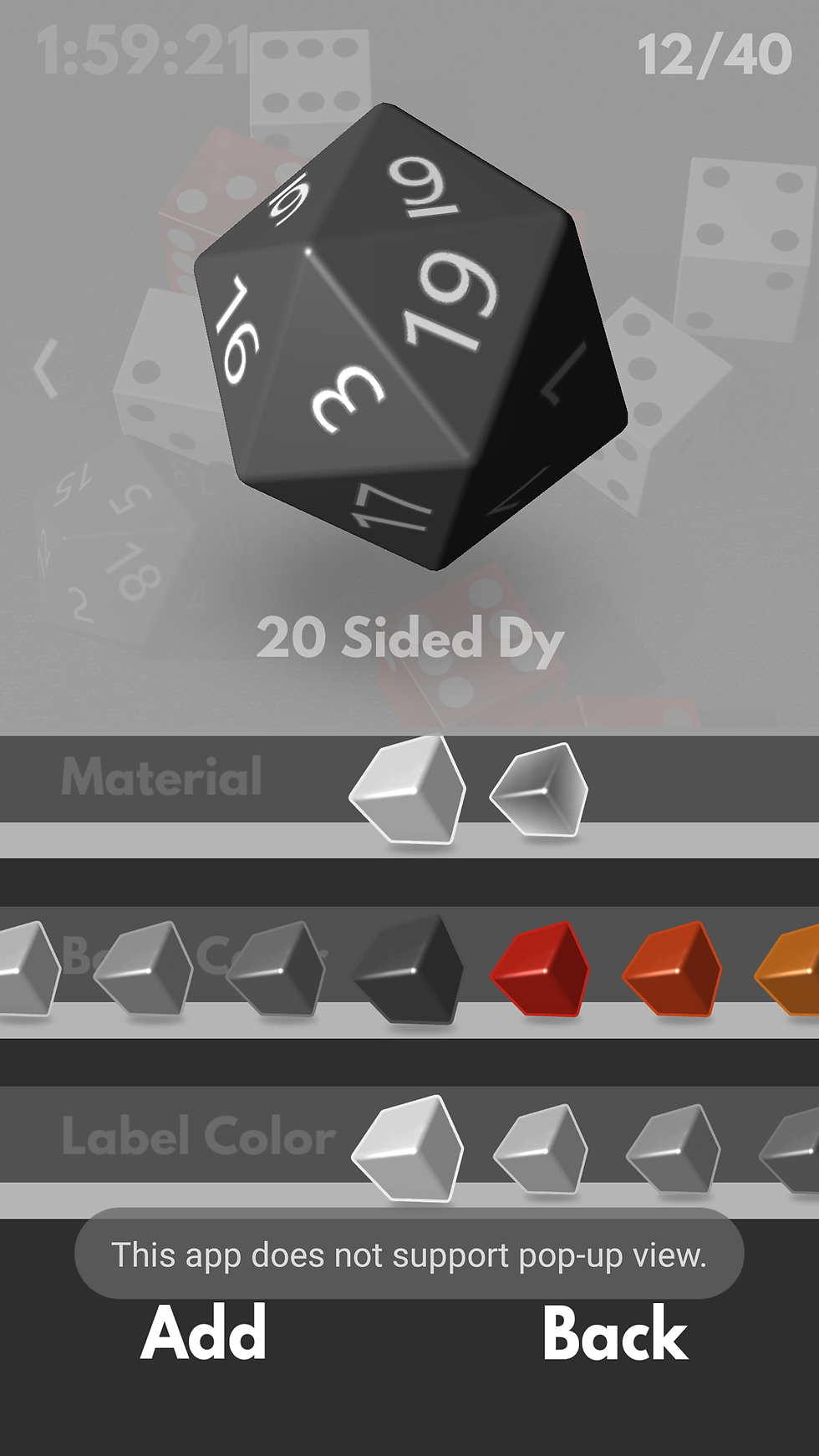
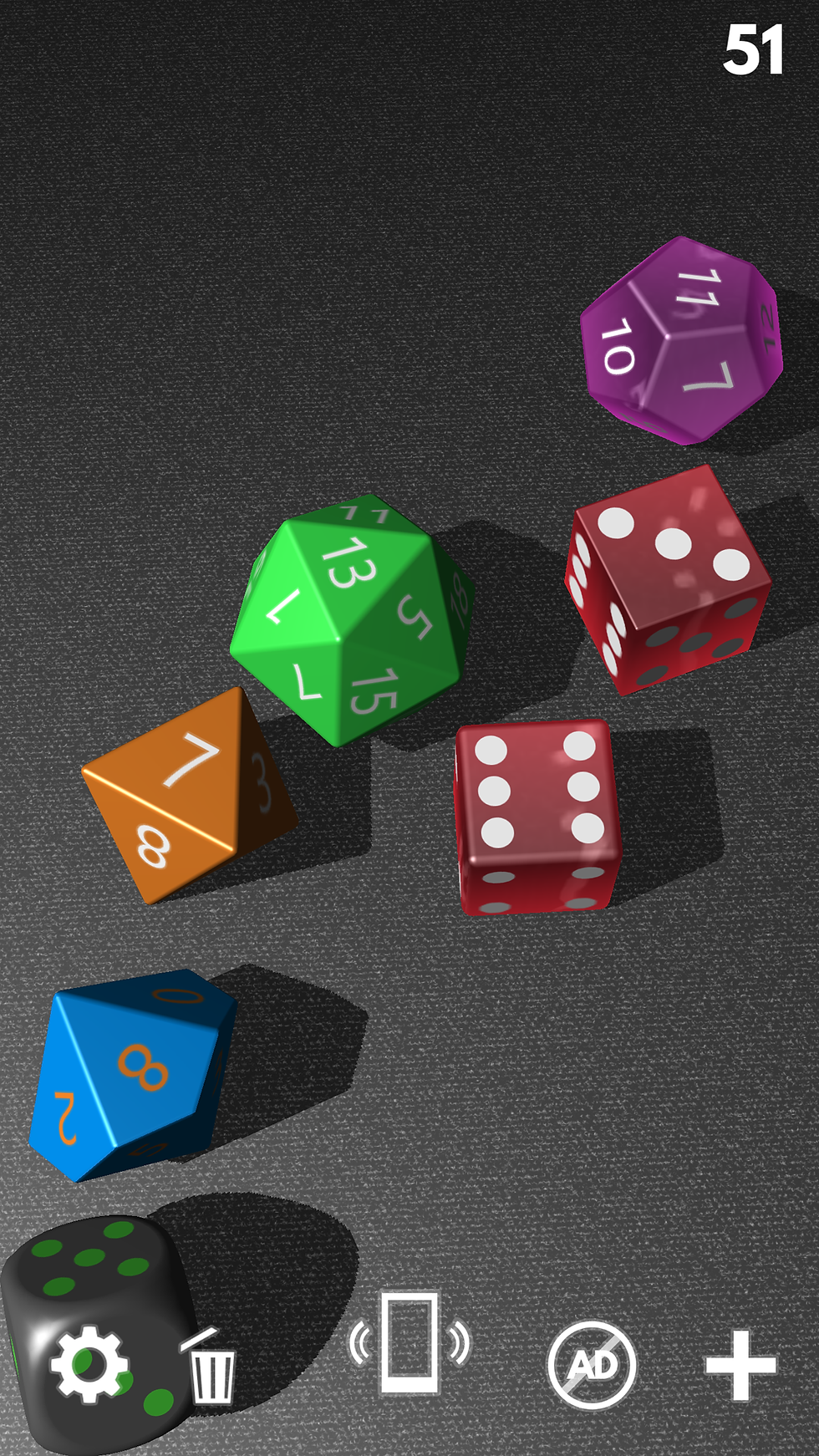
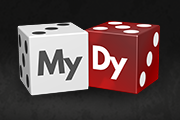



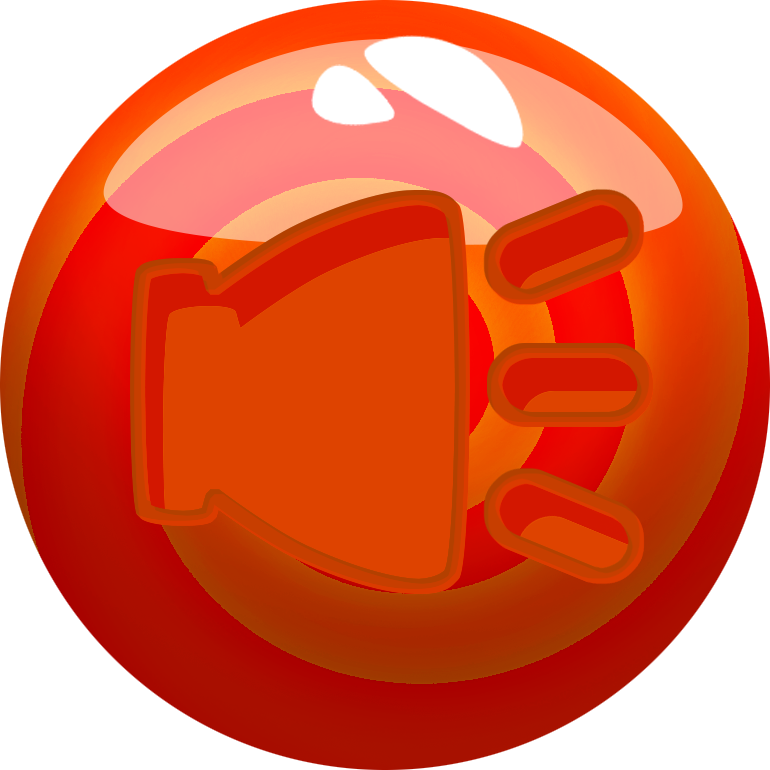


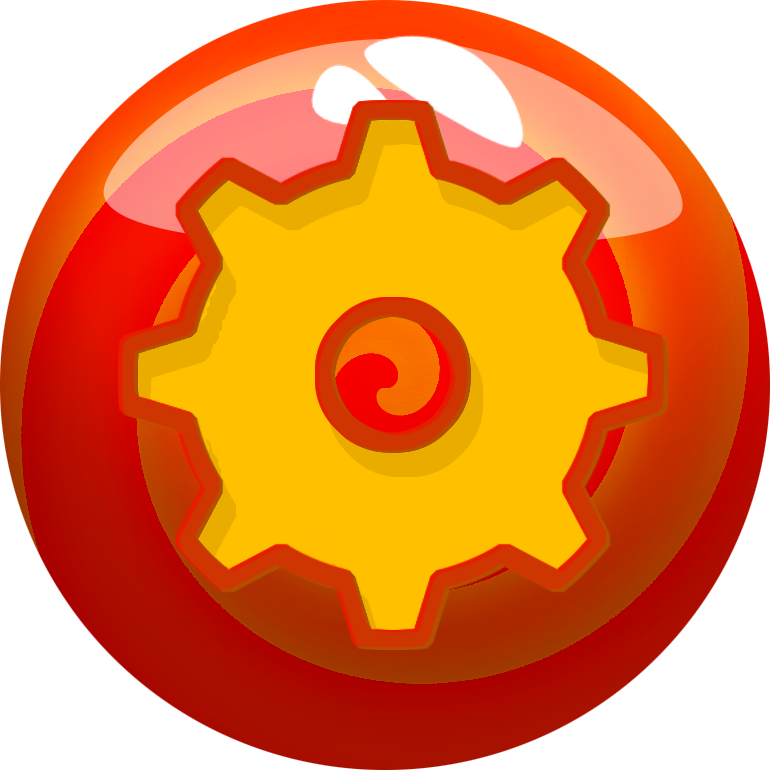









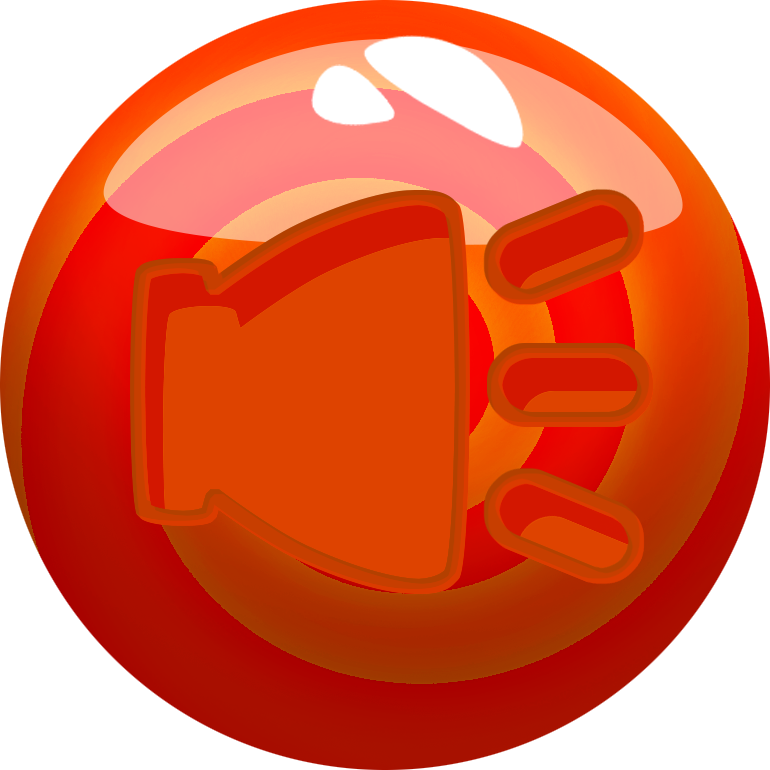


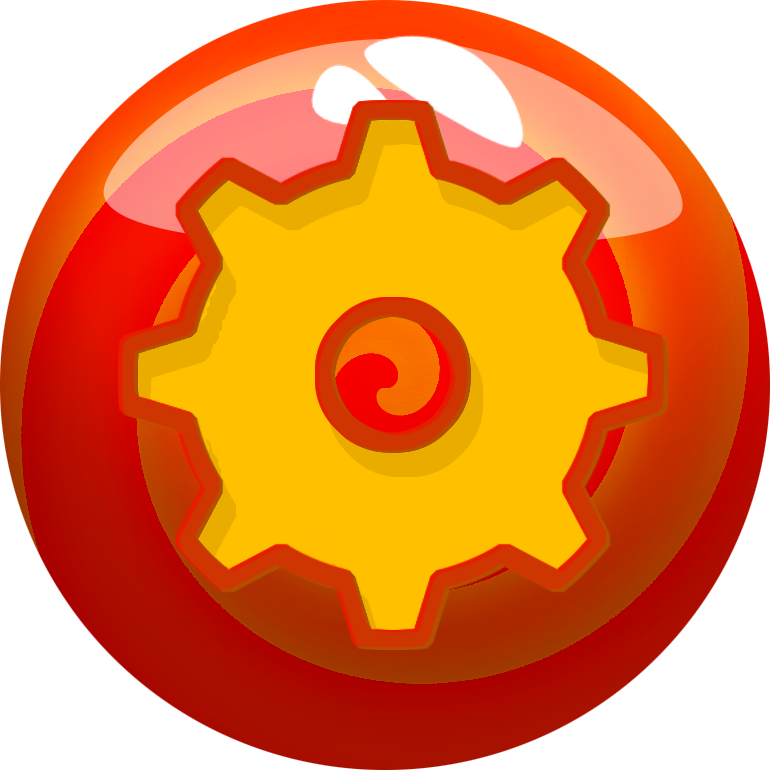










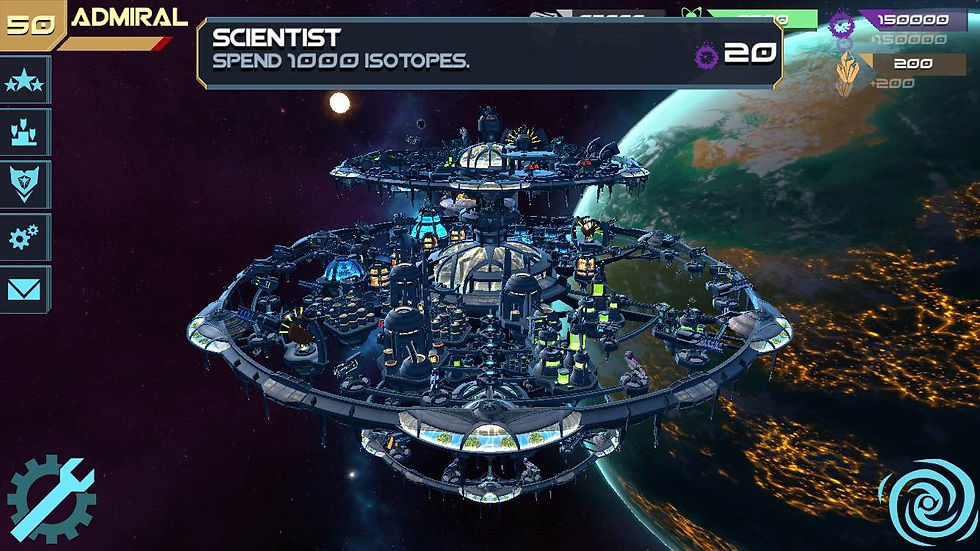
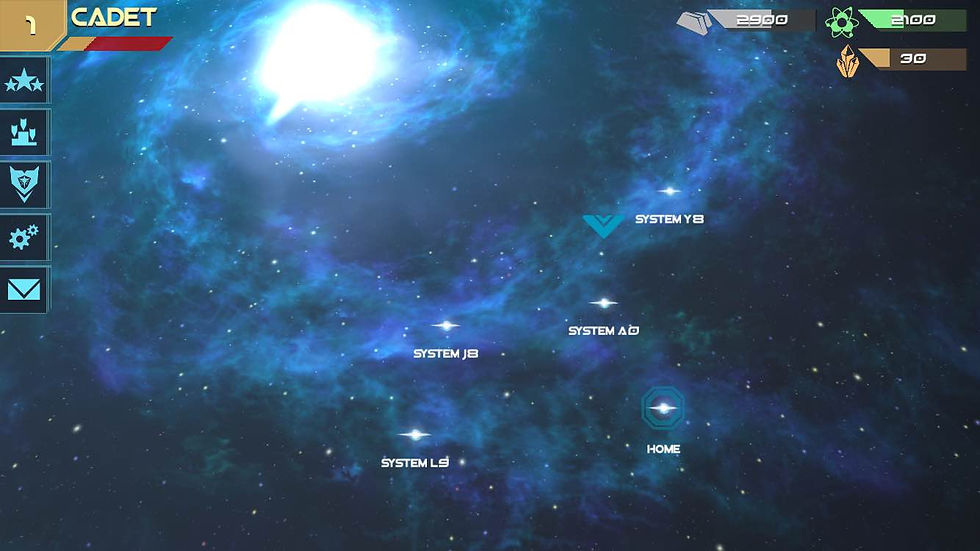
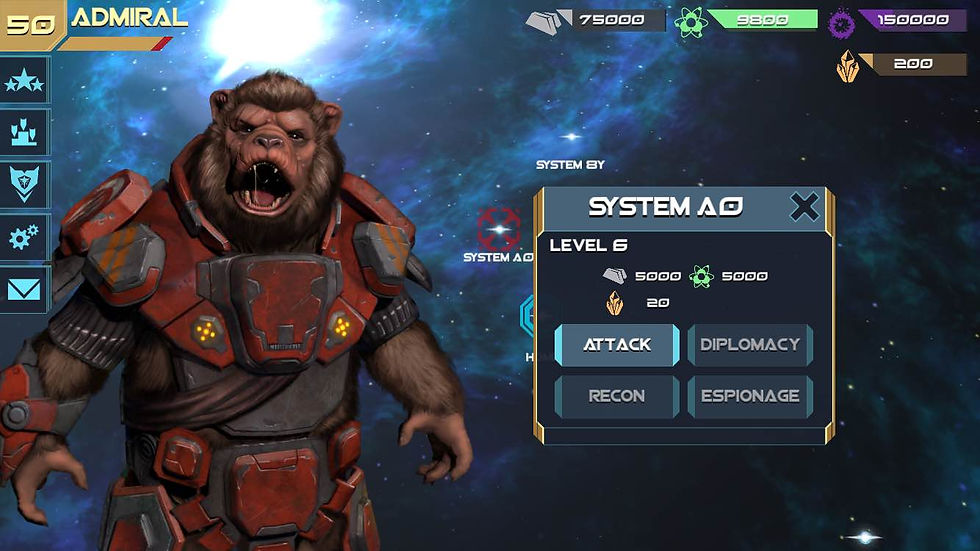

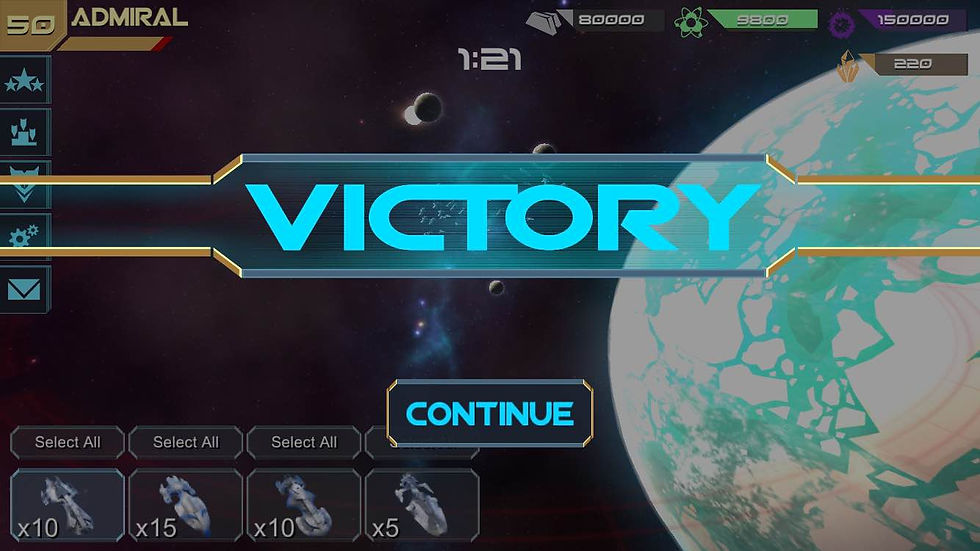




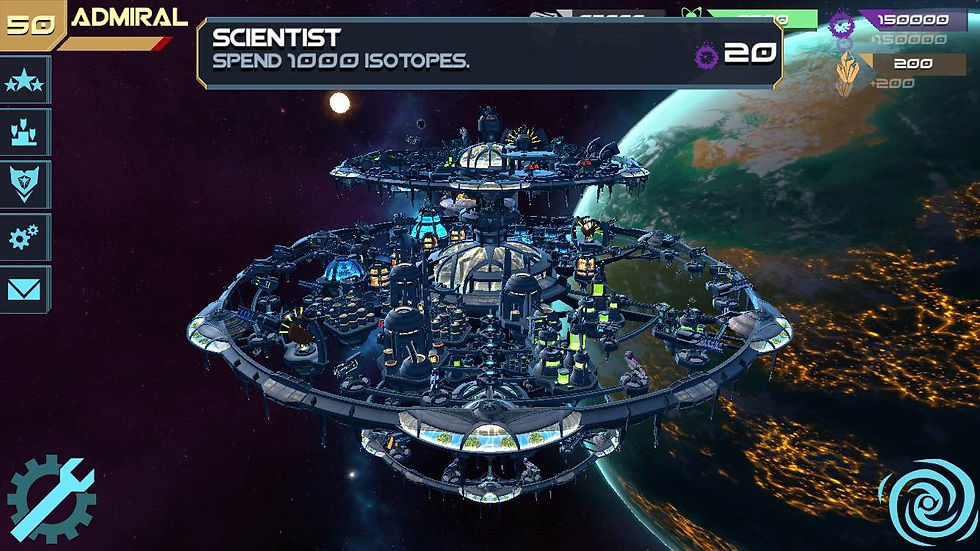
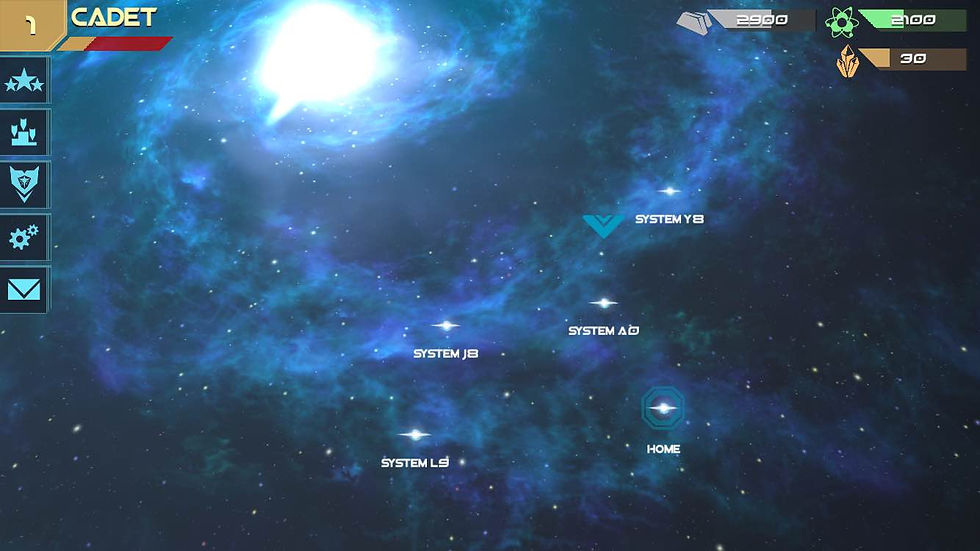
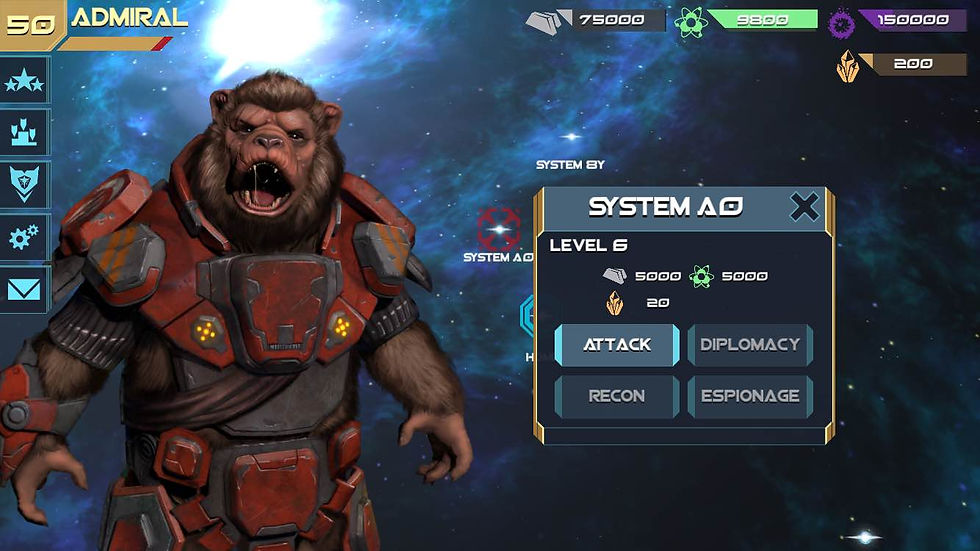

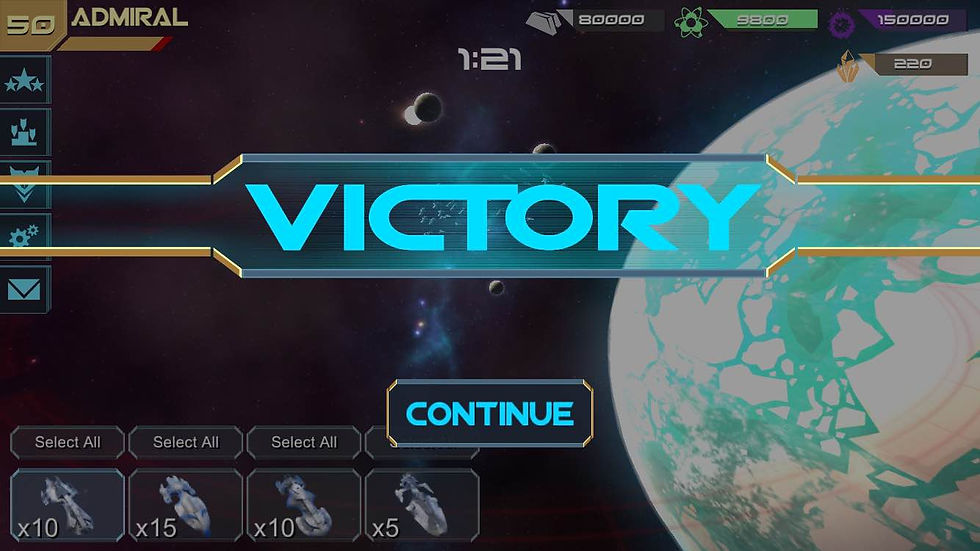
For reference I like to note that the original piece occupies positive space and is often called a positive. Also when you create a mold it occupies the negative space around the piece and is referred to as a negative. Easy enough. The lost wax process consists of an original positive, a rubber negative, a wax positive, a silica negative, and the final metal positive. To elaborate the original positive is usually created out of clay or wax, but could be made of many other materials or mediums. Rubber silicone is then applied around the original piece to create a mold sometimes requiring an outer support base made of plaster (creating the rubber negative). Typically when removing the original from the mold it is destroyed. The rubber mold is created to make multiple copies of the original using Microcrystalline Wax (wax positive). The wax positive is then fitted with a wax pour funnel and vents made from wax rods called sprues. It can look really weird but the funnel and sprues are necessary for the molten metal to travel throughout the entire mold. The sprued wax copy is then dipped in a silica slurry and covered with a layer of fine grit, dry crystalline silica. After several hours of drying, the process is repeated several times applying a progressively corser grit each
The lost wax process consists of an original positive, a rubber negative, a wax positive, a silica negative, and the final metal positive.
The original positive is usually created out of clay or wax. Rubber silicone is then applied around the original piece to create a mold with an outer support layer made of plaster (creating the rubber negative). The rubber mold is created to make multiple copies of the original using Microcrystalline Wax (wax positive). The wax copy is then dipped in a silica slurry and covered with a layer of fine grit (dry crystalline silica). After several hours of drying, the process is repeated several times applying a progressively corser grit each
time. The ceramic shell is then heated up to the point that the wax copy melts and flashes out in liquid and gas, leaving the shell empty and hollow ready for molten metal. The metal (in my case bronze) is heated to 1800 degrees fahrenheit, in a gas kiln. When it becomes molten it is carefully poured into the heated ceramic shell. When the cast has cooled the ceramic shell is removed using tools and sandblasting. A process called chasing is used to repair and work the metal to a final finish. A patina is applied, a process using different chemicals and heat to create reactions on the metals surface. These reactions create colors and textures that are then sealed with a wax varnish.